고용·원가절감·수급 안정화 효과
진입장벽 높아 정부 육성책 필요

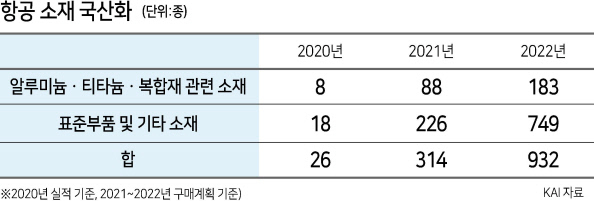
국내 항공산업이 세계 수준으로 도약하면서 소재 국산화에도 속도가 붙고 있다. 내수 활성화에 수입대체 효과, 수급 안정화까지 꾀할 수 있는 방안이라는 점에서 정부의 전폭적인 지원이 필요하다는 목소리가 나오고 있다.
20일 한국항공우주산업(KAI)과 방위산업업계 등에 따르면, 국내 항공용 소재 시장은 1조1200억원 규모에 이른다. 문제는 항공용 소재의 해외 의존도가 높아 수급이 불안정하고 비용 상승으로 이어진다는 점이다.
KAI는 이를 극복하고자 2019년부터 소재 국산화 작업에 착수, 2020년부터 본격적으로 개발에 나섰다. 소재업체, 시험기관, 연구기관, 대학 등 22개 업체가 KAI와 함께 연구 개발을 진행 중이다.
실제 성과로도 이어지고 있다. 작년엔 알루미늄·티타늄·복합재 관련 소재 8종, 표준부품 및 기타 18종 등 총 26종이 국산화를 이룬 항공소재였다면, 올해(구매계획 기준)엔 각각 88종, 226종 등 총 314종으로 10배 이상 늘게 된다. 내년엔 932종까지 급증할 전망이다.
국산화에 따른 수입대체 효과도 기대된다. 작년엔 7500만원 수준에 그쳤지만, 2023년(이후 생산계획 기준)엔 353억원으로 급증, 이후 2030년에는 2863억원 규모까지 늘어날 것으로 관측된다.
가장 먼저 국산화가 활발히 이뤄지는 소재는 알루미늄이다. 알루미늄은 항공 수입 소재의 70%를 차지할 만큼 비중이 높다. KAI는 국내 중소기업과 8개월간 개발을 진행한 끝에 국산화에 성공했다.
한국형 전투기 KF-21 사업에도 알루미늄 압출재 33종 중 6종이 항공용 재료규격서 QPL(인증제품목록, Qualified Products List)에 등재했다. 국산 소재가 항공용 재료규격서 QPL에 등재된 최초 사례란 점에서 의미가 크다.
또, 3D 프린팅 공정인 L-PBF(Laser Powder Bed Fusion, 레이저 분말 베드 융해)공정에 대한 재료·공정 규격서 등재 후 해당 사업에 4종 부품이 적용됐고, 3D 프린팅 파트에 적용되는 티타늄 분말 소재도 국산화 개발을 진행 중이다.
배관피팅, 본딩 스트랩, 고강도 인장 및 전단 볼트와 너트, 도료 등도 국산화 개발을 추진 중이다. 그 중 저압용 배관피팅의 경우 현재 18종을 국산부품으로 대체했다.
KAI는 이날 서울공항에서 열린 서울 국제 항공우주 및 방위산업 전시회(ADEX)에서도 항공우주소재 국산화 성과를 발표하고 20여개 기관과 기술 교류회도 개최했다. 진합, 한화컴파운드, 강남제비스코, KCC 등 신규 참여업체 9곳과 국산화 개발 업무협약도 체결했다.
KAI는 향후 KF-21의 알루미늄 국산화율을 높이고, 고등훈련기 T-50과 KUH, LCH, LAH 등 헬기에도 해당 알루미늄 소재를 적용할 예정이다. KAI는 국산화 대상 소재를 지속적으로 확대, 2030년까지 국산 항공용 소재를 50%까지 늘리는 게 목표다.
KAI에 따르면, 국산화 항공소재를 사용할 경우 수입산 대비 약 10~40%의 비용이 절감되고 납기 역시 기존 36주에서 25주로 30% 이상 단축된다.
높은 강도와 내구성, 내열성을 갖춰야 하는 항공소재는 기술력이 최고수준의 비밀등급으로 취급되는 등 진입장벽이 높다. 장기간 연구개발과 투자가 필수다. 소재 기술을 이전받는 것도 사실상 불가능하다. 때문에 소재업체로선 개발에 참여하는 데에 부담이 크다. KAI가 직접 항공소재 국산화 업체를 찾아다니는 배경이다.
업계 관계자는 “정부 차원의 육성정책이 뒷받침되지 않는다면 소재 국산화는 계속 요원한 상태로 남을 것”이라며 “국가 차원에서 소재 국산화를 지원 및 관리하는 기구나 조직이 꾸려진다면 항공소재 국산화 육성의 발판이 될 수 있다”고 전했다. 김상수 기자
dlcw@heraldcorp.com